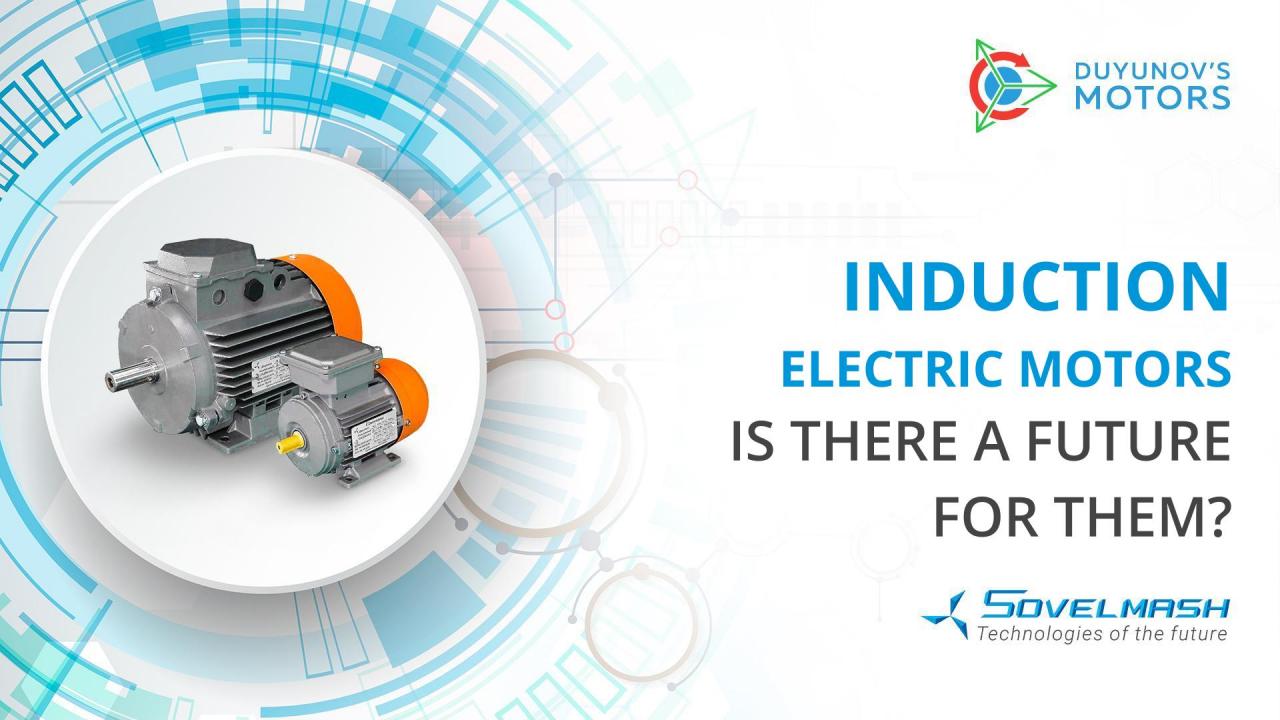
Induction electric motors: is there a future for them?
"Recently, a statement has been directed to the "Questions3333Answers" section claiming that the future belongs to synchronous electric motors. "Sovelmash" is known to work with induction electric motors, and Dmitriy Duyunov answers why he has chosen induction motors, and what is their advantage over synchronous electric motors."
Dmitriy Alexandrovich speaks about the operation principle of a synchronous electric motor exemplified by a controller. All BLDC motors require controller operation. Controllers convert direct current into currents that are fed to the motor phases. Direct current is converted from AC using a rectifier. At the controller input, there is a double half-period rectifier (diode bridge), that rectifies the sine wave. At the output we get a pulsating voltage of the same polarity, which is applied to the capacitor. The current in the circuit flows until the voltage on the capacitor reaches a value equal to the electromotive force (EMF) of the voltage source. This is how current peaks are formed. The capacitor begins to charge only at the moment when the sine wave current on the diode exceeds the capacitor voltage. That is, not over the entire sine wave, but only at a certain point in time (peak factor (PFC). In order to correct the situation, power correctors are used, which can slightly raise the peak factor. Such correctors must be installed on each BLDC motor to adjust the peak factor. But the creation of higher harmonics leads to the wires heating. And power correctors are not installed on all devices. And until this problem is solved, the scope of application for synchronous electric motors is limited.
Induction electric motors are superior in design and reliability. With moderate load, they have a longer service life. In other respects, these two types are similar in design, but different in the operation principle, thus having individual applications.
Follow our news!